Plug and direct mould milling, automated trimming
The Zimmerman FZ 35 milling machine can handle medium and large master models of tooling blocks or aluminum simultaneously on 5 axis. One of the largest table-sized machines in Hungary is capable of high-speed machining of blocks up to 4 meters x 2.9 meters x 1.25 meters. With our smaller table-size model milling machine, we perform the automated trimming and drilling of finished parts with the assistance of vacuum positioning.

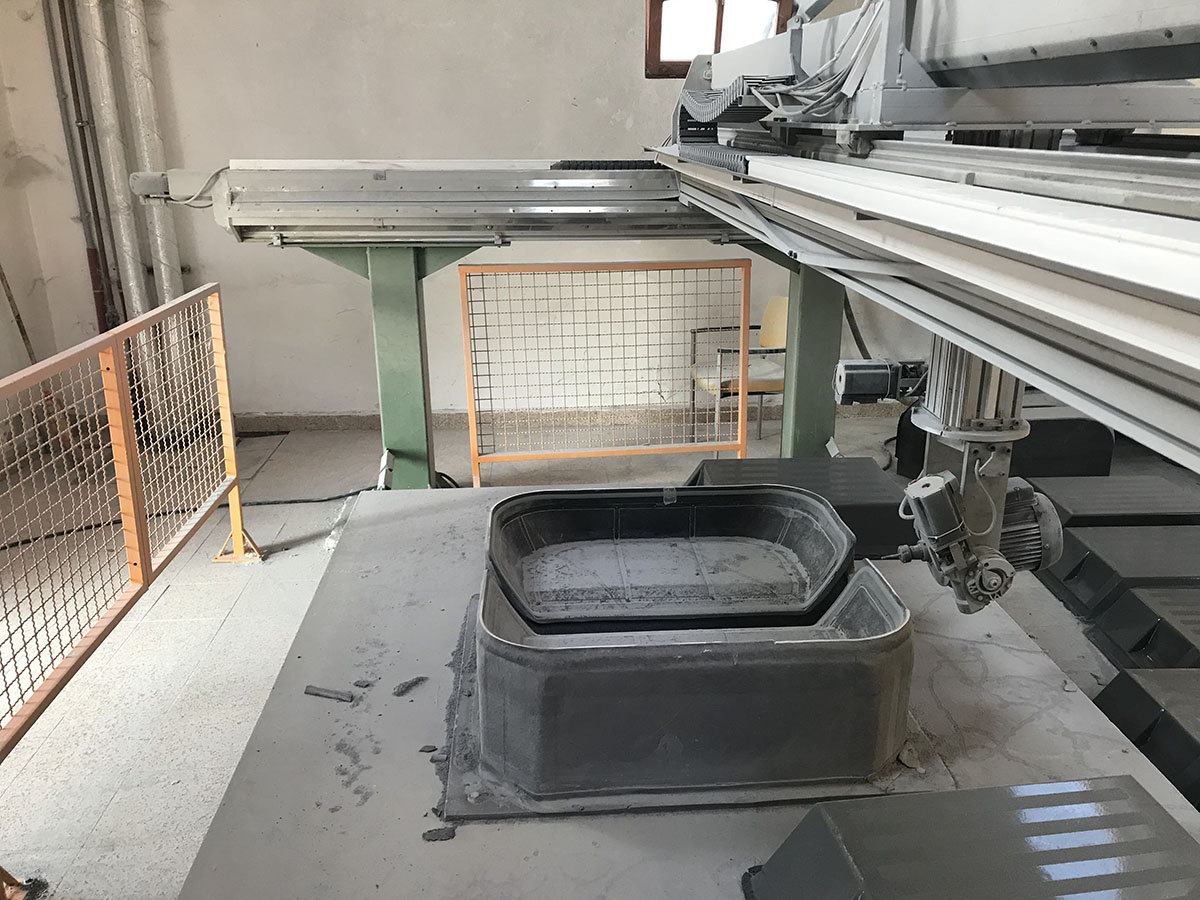
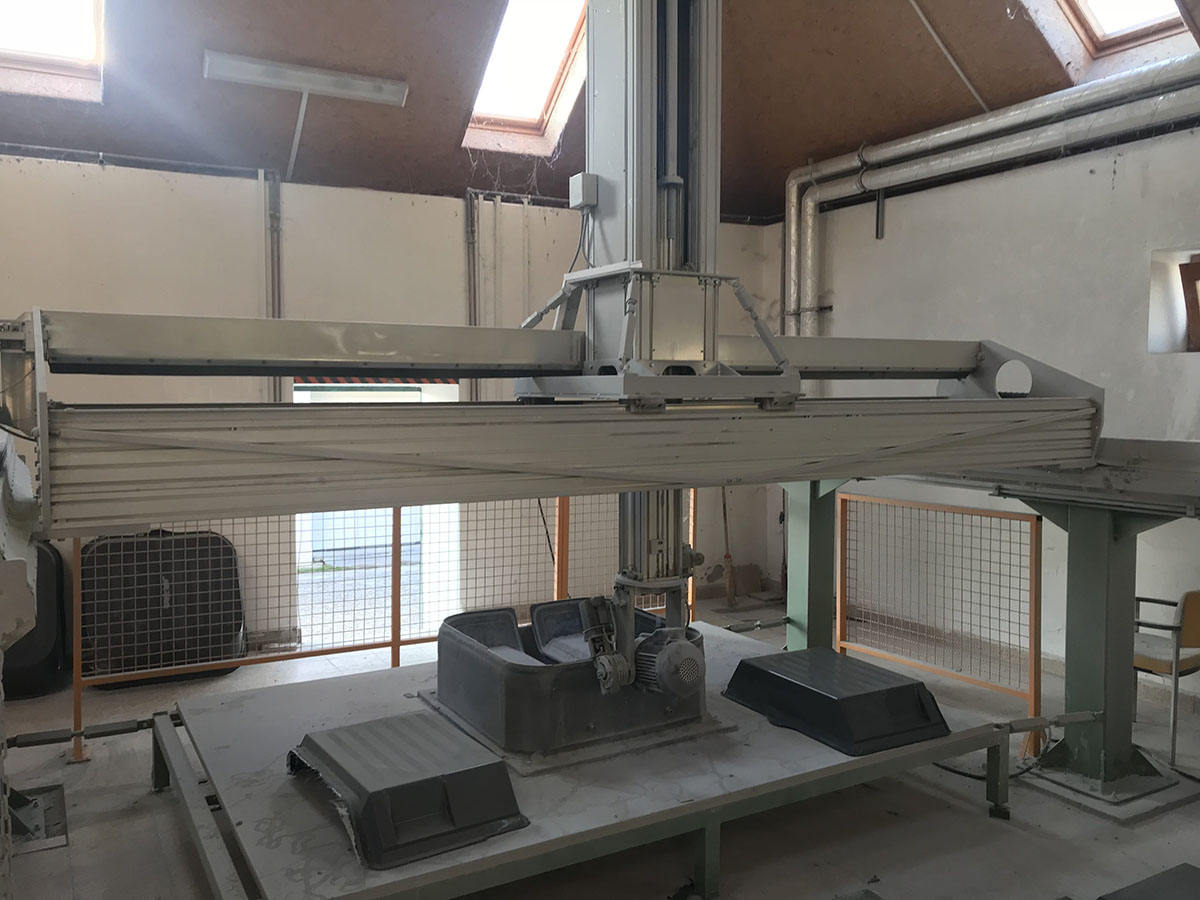